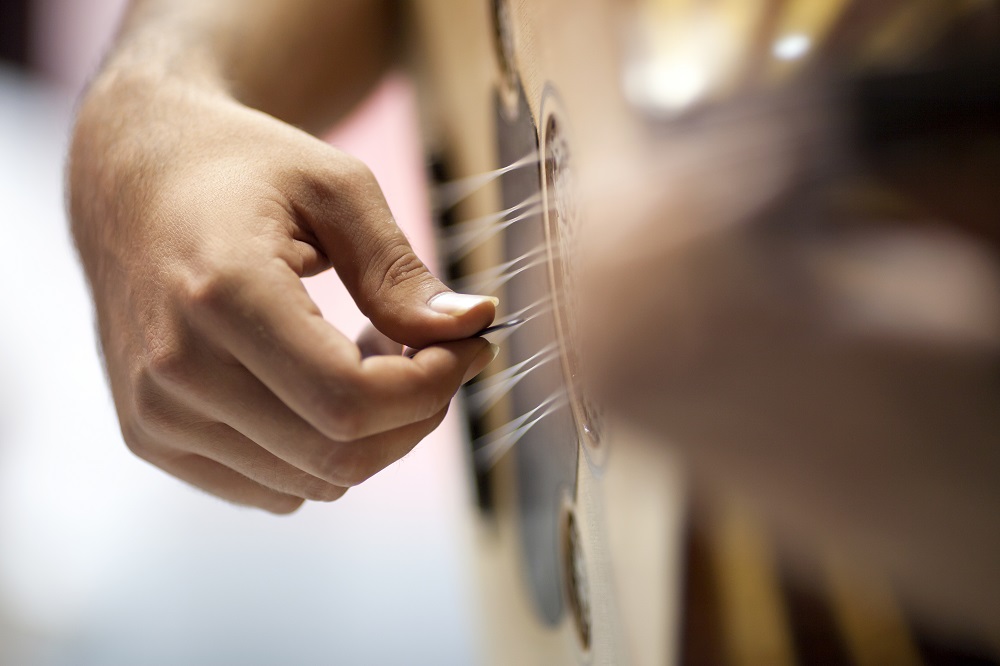
Did you know that over 2.5 million guitar strings are manufactured every day?
Curious about how these essential components of your favorite instrument are made? Look no further!
In this article, we will delve into the intricate world of guitar string production.
From the materials used to the quality control processes, we will explore every step involved in creating these vital musical tools.
So grab your pick and get ready to discover the fascinating journey of how guitar strings are made!
Materials Used in Guitar String Production
You'll find that the materials used in guitar string production vary depending on the desired sound and playability. Guitar string materials can include a variety of metals, such as steel, nickel-plated steel, or even exotic alloys like titanium. Each material brings its own unique tonal qualities to the strings.
Manufacturing techniques also play a crucial role in creating high-quality guitar strings. The process typically involves winding the chosen metal around a core wire to create the desired gauge and tension. Different winding techniques, such as roundwound or flatwound, can further affect the tone and feel of the strings.
Additionally, coatings may be applied to enhance durability and reduce unwanted noise from finger squeaks. By carefully selecting materials and employing various manufacturing techniques, guitar string manufacturers aim to produce strings that offer exceptional sound quality and optimal playability for musicians of all styles and preferences.
An interesting fact is that Fender produces a staggering 90,000 guitar strings daily! With 20,000 miles of strings each year, it's nearly enough to wrap around the entire planet.
Wire Drawing Process
When it comes to the wire drawing process in guitar string production, you'll first need to draw the wire to the desired thickness. This involves pulling the metal through a series of dies until it reaches the required size.
After this step, annealing is necessary to increase flexibility. By heating and slowly cooling the wire, its molecular structure is rearranged, making it more pliable and easier to work with during string manufacturing.
Drawing the wire to the desired thickness
To achieve the desired thickness, you can start by drawing the wire. Wire drawing techniques are used to reduce the diameter of the wire and create a smooth, uniform surface. This process is typically done using wire drawing machinery.
First, the wire is inserted into a die, which is a small opening that helps guide the wire during the drawing process. The die is attached to a drawplate, which contains a series of smaller holes with progressively smaller diameters. As the wire is pulled through these holes, it undergoes plastic deformation and its diameter decreases.
During this process, lubrication is essential to prevent friction and heat buildup. Various types of lubricants can be used depending on factors such as material type and desired finish.
Overall, wire drawing is a crucial step in guitar string manufacturing as it determines the final thickness and quality of the strings.
Annealing for increased flexibility
For increased flexibility, annealing the wire is necessary. Annealing is a heat treatment process that involves heating the wire to a specific temperature and then slowly cooling it down. This process helps to improve the durability of the guitar string by relieving internal stresses and making it more resistant to breaking or snapping.
During annealing, the wire is heated in a controlled environment to a temperature below its melting point. This allows the metal grains within the wire to rearrange themselves, reducing any brittleness and increasing its overall flexibility. The slow cooling process ensures that the newly formed structure is stable and not prone to deformations.
By undergoing this annealing process, guitar strings become more flexible without compromising their strength. This is crucial for guitarists who require strings that can withstand vigorous strumming or bending without breaking easily.
So next time you play your guitar, remember that behind each string lies a carefully annealed wire, ensuring both durability and flexibility for your musical endeavors.
String Winding Techniques
When it comes to guitar strings, understanding the difference between roundwound and flatwound is crucial.
Roundwound strings are known for their bright tone and increased playability, thanks to the ridges created during the winding process.
On the other hand, flatwound strings offer a smoother feel and a warmer tone due to their flattened surface.
The way a string is wound can greatly impact its overall sound and how it feels under your fingers, so choosing the right winding technique is essential for achieving your desired tone and playing style.
Roundwound vs. flatwound strings
Choose between roundwound and flatwound strings based on your preferred playing style and desired tone.
Roundwound strings are made by wrapping a round wire around a core, resulting in a textured surface that provides enhanced grip for players who use bending techniques or want a brighter sound. The rough texture produces more harmonics and sustain, making them ideal for rock, blues, and jazz genres.
On the other hand, flatwound strings have a smoother surface due to the outer wire being flattened. This design reduces finger noise while offering a warm and mellow tone favored by jazz, country, and vintage-style players. They also tend to last longer than roundwounds due to their smooth exterior.
Consider your playing style and tonal preferences to make an informed decision when choosing between roundwound or flatwound strings.
How winding affects tone and playability
The winding on the strings greatly impacts the overall tone and playability of the instrument. Different winding patterns can have a significant impact on string longevity. For example, roundwound strings, which have a textured surface due to their round wire wrap, tend to wear out faster than flatwound strings. This is because the rough texture of roundwound strings increases friction with the frets and fingers, causing them to lose their brightness over time. On the other hand, flatwound strings have a smoother surface due to their flattened wire wrap and are less prone to wear and tear.
In addition to string longevity, winding techniques also affect string intonation. The way in which the coils are wound around the core can influence how accurately the pitch is produced when playing different notes along the neck of the guitar. Winding too tightly or loosely can cause intonation issues, leading to notes sounding sharp or flat compared to desired pitch. Therefore, manufacturers carefully consider winding techniques to ensure optimal intonation across all positions on the guitar.
Overall, understanding how different winding patterns and techniques impact tone and playability is crucial for guitarists seeking their desired sound and performance quality from their instrument.
Quality Control and Testing
When it comes to quality control and testing in the manufacturing process of guitar strings, you need to make sure that defects and inconsistencies are thoroughly inspected.
This involves carefully examining each string for any imperfections that could affect its overall performance and durability.
Additionally, testing the tension and resonance of the strings is crucial to ensure they produce the desired sound when played on a guitar.
By conducting these inspections and tests, manufacturers can guarantee that only high-quality strings reach the hands of musicians, providing them with optimal playability and tone.
Inspecting for defects and inconsistencies
Inspect for defects and inconsistencies in guitar strings by carefully examining them for any visible flaws or irregularities. This crucial step ensures that only the highest quality strings make it into the hands of musicians.
Defect inspection is a vital part of the overall quality assurance process, guaranteeing that each string meets strict standards. During this inspection, trained professionals meticulously scrutinize every inch of the string, searching for imperfections such as nicks, scratches, or uneven winding. They pay close attention to details like gauge consistency and tension balance, ensuring that each string performs flawlessly when played.
By conducting thorough inspections, manufacturers can confidently deliver reliable and durable guitar strings to musicians around the world. Attention to detail is key in this process as even the smallest defect can affect sound quality and playability.
Testing the strings' tension and resonance
To ensure optimal performance, it's crucial to test the tension and resonance of the strings Knowing how to tell if guitar strings are too loose is important.
By evaluating the tension, you can determine if it is within the desired range for proper playability and tuning stability. This involves measuring the amount of force required to stretch the string to a specific pitch. A string with inadequate tension may feel loose and cause tuning issues, while excessive tension can lead to breakage or discomfort during playing.
Additionally, testing for resonance helps assess the quality of sound produced by the strings. Resonance refers to how well a string vibrates and sustains its tone when plucked or strummed. A string with good resonance will produce a clear and vibrant sound, enhancing your playing experience.
By carefully examining both tension and resonance, manufacturers can ensure that their guitar strings offer excellent performance, tuning stability, and string longevity.
Packaging and Distribution
The packaging and distribution of guitar strings involves carefully sealing them in protective sleeves. These sleeves are designed to prevent any damage or corrosion during transportation and storage. Packaging standards for guitar strings require airtight seals to ensure the strings remain fresh and ready for use when they reach the customer. The sleeves also provide information about the type of string, its gauge, and brand name for easy identification.
When it comes to distribution channels, guitar strings are typically distributed through various channels such as music stores, online retailers, and directly from manufacturers. Music stores play a vital role in distributing guitar strings as they have direct access to customers who need replacements or upgrades for their instruments. Online retailers offer convenience by allowing customers to purchase strings from the comfort of their homes. Manufacturers often distribute their strings directly to retailers or through wholesale distributors.
Overall, proper packaging and efficient distribution channels are essential in ensuring that guitar players have access to high-quality strings wherever they may be.
Frequently Asked Questions
How long does it typically take to manufacture a set of guitar strings from start to finish?
Typically, it takes about 2-3 weeks to manufacture a set of guitar strings from start to finish. The manufacturing timeline can be affected by various production challenges such as material shortages and equipment malfunctions, which may cause delays.
What is the average lifespan of a set of guitar strings before they need to be replaced?
On average, guitar strings need to be replaced every 1-3 months, depending on factors such as frequency of use and playing style. The average lifespan of a set of guitar strings before replacement is crucial for maintaining optimal sound quality.
Can guitar strings be recycled or repurposed once they are no longer usable?
Guitar strings can be recycled or repurposed once they're no longer usable. Many recycling initiatives exist that accept old strings for processing, while some creative individuals repurpose them into jewelry, art, or other functional items.
Are there any specialized techniques used to minimize string breakage during the manufacturing process?
To minimize string breakage during manufacturing, specialized techniques are employed. Factors such as material selection, precision winding, and quality control measures ensure durability. These methods mitigate the risk of breakage and result in high-quality guitar strings.
How do different types of guitar strings (e.g., steel, nylon, coated) affect the sound and playability of the instrument?
Did you ever wonder how different types of guitar strings affect the sound and playability of your instrument? The type of string you choose can greatly impact the sound quality and durability.
Conclusion
As you have journeyed through the fascinating world of guitar string production, you have witnessed the intricate dance of materials and techniques. Like a skilled craftsman shaping raw elements into works of art, guitar string manufacturers meticulously select materials and employ wire drawing processes to create the foundation.
Through the artful winding techniques, they bring forth harmonious melodies from these humble strands. With unwavering dedication to quality control and testing, every string is crafted with precision, ensuring that musicians can create magic with each pluck.
Finally, these masterpieces are carefully packaged and distributed, ready to embark on their own musical adventures around the world.